Forget college, be a welder and pull down the big bucks. It's a plausible fantasy perpetuated by cartoons, infographics, poorly researched articles, and even politicians unfairly pitting vocational training against the steadily rising cost of college degrees. After all, there's at least one young welder who manages serious money, $140K per year in fact. It's understandable to incorrectly assume that the future of manufacturing is all about the welding. Such a career strategy might work if you happen to entertain a Michael Bay outlook on life, where you expect to ride space shuttles for some space job flying through pew-pew explosions in exchange for bringing back 8-track tapes and refraining from paying income taxes ever again. The reality is that manufacturing employment is rapidly changing and technology is, as always, at the core of that transformation.
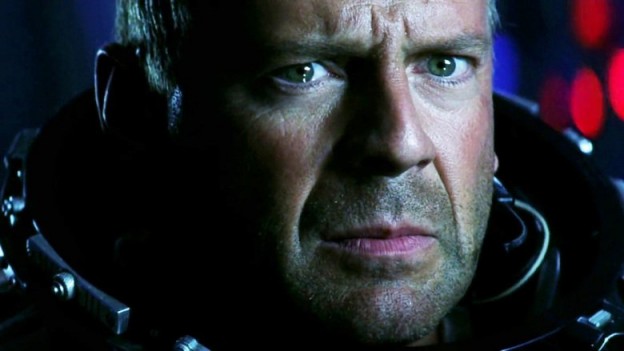
Bruce realizing that taking up welding would have been a much better alternative to making Die Hard 4 & 5.
Much ado about salaries
The notion that a skilled trade should provide more value for a student than a college degree in oh, say, the history of neoclassical basket weaving seems reasonable at first glance. So it's not all that surprising that artifacts like this cartoon (which persists in circulation thanks to social media several years after it managed to hit print) perpetuate all manner of exaggerated scenarios about highly lucrative vocational salaries, often quoted by trade schools eager to recruit. Six-figure payouts sound fabulous, but are based on edge cases, mostly a very small quantity of highly experienced welders operating in some of the most dangerous environments in the world.
Spoiler alert: quite a few of the Armageddon roughnecks end up dead, victims of action set pieces filmed from low angles. Asteroids notwithstanding, and even putting the top salaries aside, the median and starting salaries often claimed have been largely discredited.
Making this an argument about salaries, however, misses the point. There's a more important issue at hand about technical training in general, especially when many new college graduates end up either jobless or working for minimum wage. So even that basket weaving liberal arts degree is becoming increasingly irrelevant despite historical data supporting higher career salaries. The role of technology is becoming critically important for jobs moving forward, and for manufacturing jobs especially.
Manufacturing is growing; but manufacturing employment continues to specialize
Modern manufacturing is subject to a paradox: manufacturing output in the United States has never been greater, increasing dramatically over the last several decades. Yet manufacturing employment over the same period, as a share of the overall economy, continues a precipitous slide. While it may be popular to blame such discrepancies on off-shoring, such theories are unfounded. The driving force behind this reframing of industry is technological advancement. The industrial revolution is not over, it's just now going into overdrive.
Robots already do much of the welding, and will do more of it in the future. So right now the best demand for welders are where robots aren't yet readily available (like in the wilderness or underwater). But they're coming. When you think about the fundamentals of welding - the long hours, the repetitive action, the precision required, the hazardous environments, is it a job best performed by humans or robots in the long-term? I hope for your sake you answered robots.
This is a phenomenon not solely limited to welding, but many traditional manufacturing roles. Adding fuel to the welding torch, the World Economic Forum is predicting a worldwide loss of 5.1 million jobs from robots and technology over the next 5 years. The second largest area of job decline according to the report: manufacturing and production.
Technology is the differentiator
So when it comes to a successful manufacturing career going forward there are two choices:
A: develop new skills with technology
B: sabotage all the robots
The second option is not recommended, it might start a robot war. We all know how that goes.
Additive manufacturing is one of those technologies. Two ways the introduction of 3D printing helps manufacturing efficiency is reducing assembly time and cost by reducing the number of parts and sometimes reducing or even eliminating the need for tooling. What does that displace? A bunch of manufacturing jobs. By the way, guess what don't you do with a 5-piece welded assembly replaced by a single integrated 3D printed part in say, a rocket injector? That's right, weld it together.
But there are new jobs working with additive manufacturing, or robot design, or tool path optimization, or automated assembly. These are the manufacturing jobs of the future. These are the skills people should learn. Not welding. Not neoclassical basket weaving. The good news is if you're reading this, you've already got a head start.
We're making professional 3D printing easy and accessible
There's a new solution coming your way this summer. Click here or on the graphic to the left to request updates and beta access.