As I talked about in an earlier GrabCAD blog post, For Hardware Entrepreneurs and Startups, What Opportunities and Benefits Do "Smart Manufacturing" and "Industry 4.0" Offer?, "Smart Manufacturing" and "Industry 4.0" have begun improving and transforming traditional manufacturing processes and facilities.
According to Makezine, "Today’s factories...contain the coolest new tools like 3D Printing, laser cutters, robotics, generative design software and AR/VR all tied together through the Internet of Things."
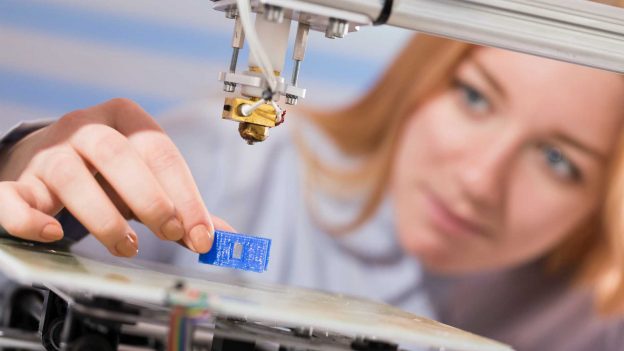
But for manufacturers looking to implement and sustain these new methodologies takes more than just adding and integrating technology. It also calls for employees with new job skills – what Sarah Boisvert, Founder, Fab Lab Hub (who was quoted in the blog post I just mentioned) calls "the new-collar workforce."
Boisvert has written a book on this topic, The New Collar Workforce, based on interviews with 200 manufacturers. The book includes Boisvert's recommendations for the types of new training programs that people will need for "new-collar" tasks and jobs.
I recently interviewed Boisvert on the "new collar workforce" – what it means for jobs and job skills, and how people can acquire these new skills, etc.
Daniel Dern: How, in terms of work force involvement, are Industry 4.0-enabled companies different from their predecessors?
Sarah Boisvert: The skills that are needed are different.
For example, typically, if you have been operating a CNC (Computer Numerical Control) machine, you are doing the same thing with it day in day out, and you have gotten reasonably familiar with how it operates, getting a feel for when there might be a problem, and how to fix many of those problems.
But these new technologies and machines are so different and new from what factories have been using for the past decades that there isn't a historical knowledge base within the company. If the company brings in a 3D printer, while 3D printing itself is 30 years old, most of the advances that make it practical for manufacturing have happened within the past five years. So there can't be somebody at the plant with 10 or 20 years of experience in solving problems with the devices.
And new manufacturing technologies, tools and methods will keep coming.
So from a skills perspective, because these technologies are changing so rapidly, manufacturers need people who are problem solvers.
Daniel Dern: In your book, you say that by 2020, U.S. manufacturing companies may be facing a shortage of two million skilled workers. How is Fab Lab Hub working to help address this challenge?
Sarah Boisvert: Fab Lab Hub focuses on training the "new collar" work force for Industry 4.0.
Fab Lab Hub has recently received funding from America Makes, the additive manufacturing institute that advances all forms of 3D Printing technology, to create Digital Badges specifically for operators and technicians in additive manufacturing.
Daniel Dern: What are "new-collar jobs"?
Sarah Boisvert: "New-collar" jobs are manufacturing jobs that also require digital skills, ranging from working with – and servicing – new computer-based tools such as 3D printers, to the programming, design, analysis and other software skills that Industry 4.0 tools, methods and processes involve.
Daniel Dern: What challenges does a new-collar job-oriented manufacturing economy face?
Sarah Boisvert: As I say in my book, "the number of appropriately skilled workers needed to fill manufacturing jobs has dwindled. Blue collar jobs have evolved into digital new collar jobs, but the training for workers has not changed."
Daniel Dern: What kinds of education do these new collar jobs involve/include?
Sarah Boisvert: Our research – looking at the operators and technicians who will run and fix the machines – shows us that manufacturers are more interested in skills than in degrees. This requires problem-solving skills, critical thinking, "deeper skills" and hands-on experience, such as "people who have taken apart 3D printers to fix them."
More generally, new-Collar jobs that involve these advanced manufacturing technologies will also require digital skills – higher level STEM (science-technology-engineering-math) and STEAM (STEM + the arts) skills than traditional manufacturing jobs.
These skills bridging the jump from "blue collar" to "new collar" are often also referred to as "Middle Level STEM Skills." "
For example, operators and technicians need to look be able to look at the design files, be able to repair them, modify design files as needed for specific machines. So CAD (Computer Aided Design) is a foundational skill to many new technologies.
And because we don't know what a lot of the new jobs will be down the road, say, in 2025, we talk about transferable skills. Critical thinking, problem solving, coding, are the basis of a lot of current technology, and these skills will also translate to new technologies. In my book, I report that the number one skill employers need is problem solving.
Daniel Dern: What are the job prospects for people who acquire new-collar skills?
Sarah Boisvert: In 2012, President Barack Obama’s Council of Advisors on Science and Technology released a report based on data from the U.S. Department of Labor, which projected an estimated shortfall of 2 million skilled manufacturing workers by the year 2020.
And a 2012 Harvard Business Review article, "Who Can Fix the “Middle-Skills” Gap?", estimated that "as many as 25 million, or 47 percent, of all new job openings from 2010 to 2020 would fall into the middle-skill range."
So the answer is, the prospects are good – and certainly better than in many other areas.
For example, one company in upstate New York needs to hire 3,000 welders in the next year, and they don't know where they are going to get them. And these are jobs in manufacturing, so typically they include benefits like health insurance, 401K, etc. That makes them good alternative options for people coming out of high school who aren't interested in going to college.
Daniel Dern: How do people looking to acquire these "new collar" skills get them? And how can they let prospective employers know what skills they've got?
Sarah Boisvert: One method that we – Fab Lab Hub, working with manufacturers, educational institutions, maker spaces, and other places – have created are "Digital Badges for New Collar skills."
(In the second part of this interview, to be published in early January of 2019, Sarah will tell us more about "Digital Badges" and how one can earn them.)
You can also learn more about 3D printing, and how to learn 3D printing skills, in the GrabCAD Groups 3D Printing Group discussion forum.