Rice University's Fred Higgs is a professor of Mechanical engineering at Rice University. He has an insightful perspective on the relation between Industry 4.0 and the ongoing 3D printing evolution. His views and explanations stem from a podcast sponsored by the University of Notre Dame this past year.
What is Industry 4.0?
Industry 4.0 refers to the fourth industrial revolution, is a moniker for an unprecedented development with automation and connected devices, within systems and equipment, to connect, and provide a whole new pipeline of information.
At the bedrock of Industry 4.0 is complex wiring, digitization, and new sensing technologies that provide a crucial link between inputs (often analog) and outputs (often digital). And this automation is expanding and growing in capability and complexity.
According to McKinsey & Company in their report "Digital service excellence: Scaling the next-generation operating model," the permeation of the Industry 4.0 is taking full embrace. It's the new and exciting approach to everything from smart vehicles to smart factories, smart buildings, and just about smart everything. It is at the core of a newfound digital revolution that uses automation and sensors to perform all types of iterations. Says McKinsey in the report:
The Fourth Industrial Revolution is no longer hype; it has fully arrived and is now enabling real gain in productivity, sustainability, agility, and speed to market. However, many companies are still struggling to build on early pockets of success in a way that delivers meaningful improvements at scale and across the enterprise. There are signs that next generation operating models are emerging within traditional organizations, but the pace of change still significantly lag the broader adoption of digital capabilities happening around the world.
Matching Additive Manufacturing with 3D Printing
Industry 4.0, albeit a digital revolution, also incorporates many facets of additive manufacturing and 3D printing.
The digital facet of Industry 4.0 has lot to do with the automation of the factory floor and the production of goods from digital files. That's where 3D printing syncs well. It enables customization on the same factory floor that can produce widgets.
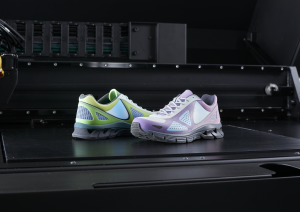
Prototyped shoes created on a Stratasys J750
As Higgs explains, you have a three-dimensional computer-aided design file of something that you are trying to print from a three-dimensional CAD file. Instead of a "subtractive" machine such as a CNC milling machine or lathe, or an injection molding machine that can churn out plastic products and forms, you now have a new machine - a 3D printer. You can feed a digital file to a 3D printer program. Layer by layer it produces a product - which may be customized if you like - using automation to guide it, just as you would for proverbial manufacturing. Suppose one wanted to produce a customized pair of shoes specially made to foot?
"Okay, they're size 13," explains Higgs. "Let's solidify the powder in this area. And so they make a thin layer that shows the imprint of the bottom of my feet. And then the next layer goes up. Now it's a little bit of, you know, a percent, small percent of my shoe, and then it goes up--or I should say, let's stick with my body, it's the next layer of my foot. And it just goes up in slices. If you do that, there's no reason you can't have holes in the middle of it and make little tubular geometries inside of it, little veins and things like that, if you had a printer that could do biological material. There's just no reason why you couldn't. So, there's no limitation to the design complexity because it's additive."
The Dexterity of Industry 4.0 Automation and the Versatility of 3D Printing Is a Boon to Medical Manufacturing
"My father got an artificial knee several years ago," explains Higgs. One size fits many. I'm not gonna say it's one size fits all, it's one size fits many. My father is about 80 years old. He walks a certain way. He has a certain gait motion. All these variables can be considered to give him a custom knee. If all things being equal in the manufacturing process, then let's make one for my father. So it's a personalized knee that we're after.
Higgs says the precision of additive manufacturing permeates into numerous medical applications. He cites the example of a cancer patient needing a hip replacement. "You can be custom. Forget the type-one, type-two, type-three cut. "
You can alter the CAD file for one individual and print a custom hip joint. "We have models that for each project have the different modes of physics that govern the performance of that particular product you're trying to build," he explains. "We take that performance into account to do this analysis. We get a winning candidate, and then we print it out. Whether it's a drill bit, or it's a hip or a knee like what my father has, it comes down to getting patient-specific information, running some analysis that shows you which winning design is personalized for that patient, and now you can do it for a lot of people. You have mass customization, not mass manufacturing."
If you would like to learn more about Industry 4.0 and how that can impact your additive manufacturing operations, GrabCAD offers a free AM evaluation where you can speak to a PM to learn how you can scale and maximize your production.