Model Shops are not cheap operations. Just using 3D printers and their materials are expensive. When your job is to produce parts/prints for customers or internally, the price of fabricating all those requests can add up. What makes the costs manageable however are effective printing, scheduling, and managing of assets within a shop.
Not having these practices in order is a recipe for your shop going under. Below we are going to cover 5 things you're doing wrong in your model shop that’s costing you money.
Not organizing your printers when scheduling
3D printers can vary in technology, build size, material type, and speed to name a few. Even if you only had duplicates of a single type of printer, poor scheduling can lead to a pile up in your 3D printing backlog.
Poor scheduling can manifest in the many forms but are not limited to:
- Over assigning jobs to a single/set of 3D printers
- Incorrectly assigning a job that requires a different printing technology
- Sending a job to a down/printer in use rather than an open printer
A solution to a lack of organization in your printer fleet is to first understand your current printer capabilities and organize them based on physical attributes like technology or build size. Another way to achieve better organization is having printers reserved for specific types of jobs while keeping other printers more flexible in the types of jobs they receive.
Ordering excessive amounts of material
3D printing materials possess expiration dates like ink printer cartridges. Choosing to use expired materials can have detrimental effects on your 3D printer such as increasing the chances of jams occurring while loading/unloading said materials or while printing itself. This is something that FDM printers in particular can suffer from due to these printers using filament to print. A jam could set your job back a few hours to a few days depending on how bad the jam is.
Even if nothing bad were to happen when printing with expired material, your final part could suffer from quality issues. The most glaring outcome is that your part could come out weaker or have poor looking aesthetic features. If the condition of the expired material is bad enough, what might even happen is that you might be forced to throw it away which all contributes to money being lost.
Identifying how much you print on a monthly to yearly basis to establish a baseline can lessen or even eliminate the risk of printer materials expiring because you only end up purchasing what you need for your jobs. This start to tracking 3D printer material usage can ultimately lead to money being saved.
Not properly calculating the cost of a job
Understanding what is needed to complete a 3D printing job and how much it costs should be one of the most important aspects to consider when running a 3D printing shop. Not calculating the costs of one or multiple jobs can have a ripple effect that impacts the amount of 3D printing materials you purchase, how often / what types of jobs you accept, and whether or not you can expand as a business.
A basic formula for calculating these jobs can start with identifying the technology of the printer being used, the material used to create the part, and the post processing needed for final assembly or delivery. Having these aspects calculated plays a part in managing not only the print shop or business as a whole, but also has benefits even if you are a hobbyist.
Not tracking the progress of your jobs
This is the second half of overall scheduling of one or more 3D printing jobs. Keeping track of the progress of one or more jobs is integral to allowing a 3D printing shop to operate at its best. Having a process established when requesting a job can reduce an immense amount of stress on the printer technicians, the person managing the printer shop, and the person who is to receive the finished product.
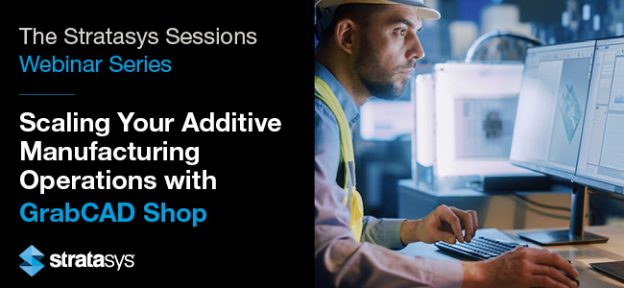
If you would like to learn more, check out our latest webinar in which we dive into the abilities of GrabCAD Shop and how professionals within additive manufacturing can benefit from this powerful solution.
By not keeping track of your jobs, a number of these issues can occur:
- Parts finish printing but stay on the tray which blocks a printer
- A part gets duplicated on another printer
- Too many prints finish but need post-processing
- Parts never get printed because there is no priority set
- A part gets to the intended person but is unfinished
- Your job request got lost during the process
There are ways to track jobs and where they are. Some people use spreadsheets to track the progress of their jobs in the workflow, others just communicate via email or other form to convey a job’s status. This is a manageable solution if you are a very small business and have no interest in expanding however there is an easier way.
Not using a software that allows you to expand your operations
To be fair everything stated above is not easy to accomplish as a small team much less as an individual. Each solution I have given can only work as well as the people who are in the shop. Implementing these more positive printing practices can alleviate some of the pain and money lost but these tips are only the start. There are software solutions that exist that are meant exclusively for 3D printing model shops. These work order management systems simplify the scheduling of jobs, allow for the calculation of 3D printing shop assets and costs, tracking and more.
If your time was freed from having to contend with all of these aspects on a weekly to monthly basis, you could start considering expanding your printing business. For example, more 3D printers and materials could be added to your fleet to accommodate more jobs. The types of printer technologies could also expand because you now have the infrastructure to track different types of technological jobs. You could scale your business to be as large as you want without having to worry about growing too large to manage.