Additive manufacturing is projected to have another big year in 2023. In fact, according to industry reports, additive manufacturing is expected to grow at 20% to 22% annually for the next five years.
Why? Because additive manufacturing continues to play a vital role in helping manufacturers overcome supply chain delays while also empowering them to get (better) products to market faster.
And it’s not just one particular industry; according to Diogo Quental, Global VP of Strategy, Partnerships, and International Business Development at Raise3D, the industries that will see the most growth this year include defense, automotive, dental and aerospace.
So let’s dig a little deeper and see what exciting trends 2023 has in store!
While the COVID pandemic offered opportunities for 3D printing to rise to the occasion, there was the juxtaposition of the subsequent global industry downturn in the years that followed. Add in factors such as uncertainty over fuel prices, supply chain disruption, the increasing cost of living, rising production costs and the continuing war between the Ukraine-Russia, and you’re left with somewhat of an unpredictable landscape.
According to Markus Glasser, Senior VP at EOS ,“3D printing materials, hardware, and services sales combined will rise from $12 billion in 2021 to an estimated $38 billion by 2026.”
Shifting supply chains
Looking back on the past few years, it’s important to note how 3D printing was able to help with breakdowns in the global supply chain. The COVID pandemic, for instance, showed how valuable additive manufacturing solutions were, particularly the rapid production of 3D printed face masks and shields. Stratasys, for instance, with the help of many partners was able to make over 100,000 face shields for hospitals, medical personnel and other first-line responders.
Similar ventures were taken on by companies across the globe, as the production of mask adjusters, temporary emergency isolation spaces, hands-free door openers, test swabs and respirator parts became a priority. Movements such as the ‘innovate2ventilate’ project encouraged widespread community innovation and ingenuity like never before in the 3D printing world.
Today, additive manufacturing continues to play a big role in supply chain management. The technology removes the need for excess physical spare parts (as these can be stored digitally) and enables extra products to be produced quickly if necessary too (as seen during the pandemic).
Companies can therefore better manage their products from the get-go, reducing both waste and costs.
With new 3D printing materials coming to the market, an increasing range of printers and a growing number of additive manufacturing methods available, it makes sense for many companies to outsource certain aspects of 3D printing to companies who specialize in those areas.
According to Marketverse, “Simplified supply chains make a lot of sense for companies needing small batch production for rapid prototyping, spare parts, tooling, jigs, and fixtures.”
On the other hand, some industries and companies are looking to do the exact opposite and bring 3D printing in-house. For instance, 3D printers are popping up in hospitals, dentist offices and especially classrooms.
New materials
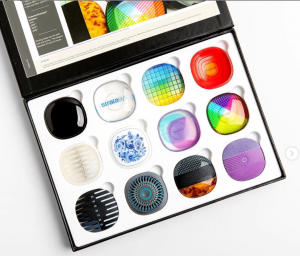
Photo courtesy: Stratasys
2023 will see new materials (with new mechanical properties and new capabilities) at the forefront of 3D printing. Watch the metal additive manufacturing and bio-printing spaces in particular.
We’re also likely to see additive manufacturing be taken up in new sectors and therefore witness innovations with regards to suitable materials for those industries. Flexible electronics, energy production and lifestyle/well-being products are just some of the areas set to experience a manufacturing renaissance with 3D printing at the heart.
“Outside of the high cost of the equipment, the next big barrier is materials and closed additive manufacturing ecosystems, which have stymied the 3D printing industry’s growth. Numerous types of 3D printing materials are on the market today, but few are advanced enough to meet the quality or regulatory requirements of industries." -- Design News
Increased 3D printing education
As additive manufacturing is adopted by more industries and businesses, increasing numbers of professionals need and wish to learn about the technology. 2023 will undoubtedly see more widespread adoption of 3D printing training and upskilling, particularly in remote online and virtual course format.
There is likely to be a greater number of specific courses focusing on in-depth knowledge of additive manufacturing in certain industries and key areas within those industries.
Better sustainability
In the context of climate change awareness and various global government initiates, reducing environmental impact is (or should be) at the top of the agenda for all industries and manufacturers. While attitudes do vary globally, I have no doubt that 2023 will see these efforts continue to ramp up in the 3D printing sector via new solutions and an influx of innovation from those within the sector.
More industries will look to additive manufacturing to:
- Harness lower energy consumption.
- Reduce waste and fewer required materials (many of which are both lighter and recyclable).
Not to mention the fact that entire assemblies can be printed in one go (vs printing multiple individual parts).
The 3D printing industry itself, while inherently more ‘eco-centric’ than traditional manufacturing methods, is also under pressure to make improvements where possible too. For example, polymer 3D printing might not be considered at the go-to method unless there is some sustainable aspect to the project such as sustainable materials or plans for recycling of products. There is also mounting emphasis being placed on streamlined workflows.
Transparent sustainability is on the minds of customers too. They are increasingly expecting for services, products, packaging, and methods of production to have minimal global environmental impact (and to be able to prove it). Provable sustainability is therefore something that additive manufacturing companies and companies relying on the technology will have to consider.
Greater customization & automation
Customers are demanding more personalization when it comes to products and services and additive manufacturing enables this concept to thrive. No doubt we’ll definitely see more of this over the next year. In addition, the ability for additive manufacturing to produce large volumes of product components via automation will also likely increase in 2023.
Automation, largely achieved via AI, enables companies to:
- Save on costs
- Improve workflows
- Provide better health and safety protocols
- Ensure product quality standards are controlled and maintained
Put these trends together, and you’ll be seeing more products produced to a higher quality via 3D printing thanks to automated order management, the printing process itself, material management and post processing, but with the added ability to customize before purchase.
Talk about win – win.
Looking ahead
3D printing’s popularity is gaining in traction year-over-year, not least due to the reduced design and production times, as well as increased overall quality of end products. While additive manufacturing might not replace traditional manufacturing in certain instances, it does provide access to faster prototyping along with cheaper spare parts and customized tool production.
As with all industries, additive manufacturing is impacted by the varying global matters at hand. However, if the past few years are anything to go by, then 2023 will see the world of 3D printing continue to break down barriers and rise to the occasion.
Supply chain interaction, newly explored materials, continued upskilling, sustainability opportunities, increased customization and greater automation are all key trends to monitor in the additive manufacturing world. Let’s see what the next 12 months brings!