In my previous blog post, I provided an overview of what compliance certifications like UL, FCC, CE, and RoHS are, and what ones your new hardware product may need.
In this post, you'll get a sense of how much time and money your product planning should factor in to get them, along with other advice.
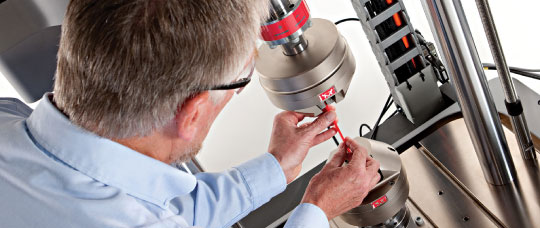
Getting all the necessary compliance certifications for your new hardware product can be costly and time consuming.
Compliance Isn't An Afterthought, It's a Key Ingrediant From the Start
Compliance isn't something like bubble-wrap or a coat of paint that you add in at the end. A problem that isn't discovered until you've build 10,000 units means you've got to fix – or throw out – all of them, then correct the manufacturing, which may involve retooling and a redesign.
"The single best thing to do is incorporate safety and compliance into the product development process," stresses John Allen, President, Product Safety Consulting, Inc., which provides product developers and manufacturers with expert advice and testing services, including for product safety and regulatory compliance. "You should start from concept. A good compliance engineer can get the team going in the right direction from concept sketches. The sooner you start, the less pain, additional expenses, and delays you'll feel later on."
How Much Do Compliance Certifications Cost?
Meeting compliance regulations and obtaining certifications aren't "additional costs." They are part of your baseline budget – because you can't go to market without them. These costs will include having compliance experts/expertise as part of the product team, plus internal or external time to acquire, fill out, submit and track paperwork and fees for submission and testing.
Large companies with lots of products, models, and versions can easily spend millions of dollars annually ensuring compliance and receiving certifications – if they have lots of products, models, and versions.
On the other hand, if you're creating only a few specific products, and are initially targeting well-focused geographic and industry markets, the cost to satisfy and obtain the requisite certifications are likely to be between $10,000 to $25,000. Although, notes Product Safety's John Allen, "If you're global, and wireless capabilities like WiFi and Bluetooth are involved, it could easily go higher, even to $100,000 and over."
For example, Allen says "for an electric drill intended to be sold in the United States and Canada, expect to spend roughly $8,000 to $12,000 – if you pass the first time through. If you want to sell internationally, add another $3,000 to $6,000 for IECEE CB Scheme certification."
Similarly, for a computer intended to be sold in the United States and Canada, according to Allen, allocate an estimated $5,000 to $8,000. For the CB Scheme certification, add another $2,000 to $5,000.
And, Allen adds, "If you don't have the resource internally to do the work correctly, add $5,000 to $7,000 for outsourced consultants."
Compliance Certifications Also Add Time
Qualifying for and obtaining compliance certifications doesn't just involve money, it also involves time and timing.
Ensuring your product will be compliant can add time and work to the design and prototyping processes, but far less time to address concerns during design than after the prototype, or the first manufacturing run, is done. Additionally, sending your product off to be examined and tested takes time.
"Lead times with most testing labs are six to 12 weeks if you pass the first time through," says Allen. "Any 'non-compliance issues' – like failing to pass or otherwise qualify – will add additional cost and time to every project."
Bill Drislane, SVP of Manufacturing and Engineering, Dragon Innovation, a manufacturing services firm that works with entrepreneurs to launch hardware products and scale companies, says, "We know of products whose schedule has been delayed months through failure to pass required tests. Much redesign and retesting was required to finally gain certification, and as a result the product launch was delayed and the whole project was under a great deal of stress."
Getting Help: Look to Your Business Partners
Even if you've gone through the compliance drill previously, if you're a start-up you'll need help.
- Do your homework. Read the appropriate standards and related requirements documents, so you become familiar with what to do and what will be involved.
- Look for engineers with relevant experience.
- Pick components and suppliers that already have required certifications.
- Look to your partners for expertise, advice, and consulting services. This includes crowdfunding sites like Kickstarter and Indiegogo, and suppliers/manufacturers like Arrow Electronics, Dragon Innovation, and HWTrek who have gone through these processes with many small (and large) companies and products and have a vested interested in your product's timely, cost-effective market availability.
- Many of the testing laboratories also offer related consulting services.
"Don't cut corners when safety is an issue," says Dragon Innovations' Bill Drislane. "A single safety recall can kill your company. Given this, if your product plugs into the AC supply, or has a large lithium-ion battery, then UL certification or its equivalent can help you sleep at night and know that you have done all you can.
Oh, and one last tip: plan for success.
Don't forget during the design phase to reserve appropriate space on your product cases, documentation, and packaging for the certification icons!
Like what you've just read? Sign up to receive GrabCAD's free weekly Digital Thread newsletter.