Jenni Stuart is a Boston-based jeweler who specializes in high-end fabrication and custom fine jewelry design. All of her pieces are uniquely original, and meticulously crafted – mostly by hand, but Jenni also started using CAD a few years ago to help speed her design process.
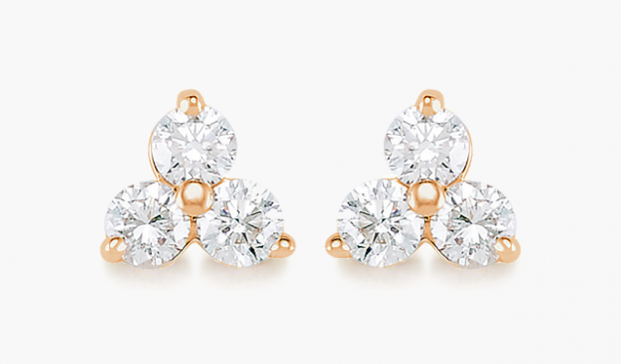
Custom diamond studded designed and crafted by Jenni Stuart.
In fact, Jenni learned a lot of her CAD skills, tips, and tricks on the GrabCAD Community. We spoke with her recently to see how she uses GrabCAD to help make her job easier:
Dave Moran: Tell me about yourself and how you got into jewelry design?
Jenni Stuart: I was the weird art kid in high school and I had really supportive parents who were wonderful, but knew I needed to make some type of reliable life plan. I took a lot of courses in different mediums and wound up doing an early college program at Maine College of Art in Portland, Maine. I thought I wanted to do photography, but that elective was full so I did jewelry.
It was awesome, I loved it, and I went home and my parents agreed to buy me a blow torch and an anvil and I just never looked back.
I went to Pratt Institute in New York City and I’m a classically trained goldsmith. I’ve done mostly hand building, I was trained to fabricate jewelry by hand from scratch from raw materials.
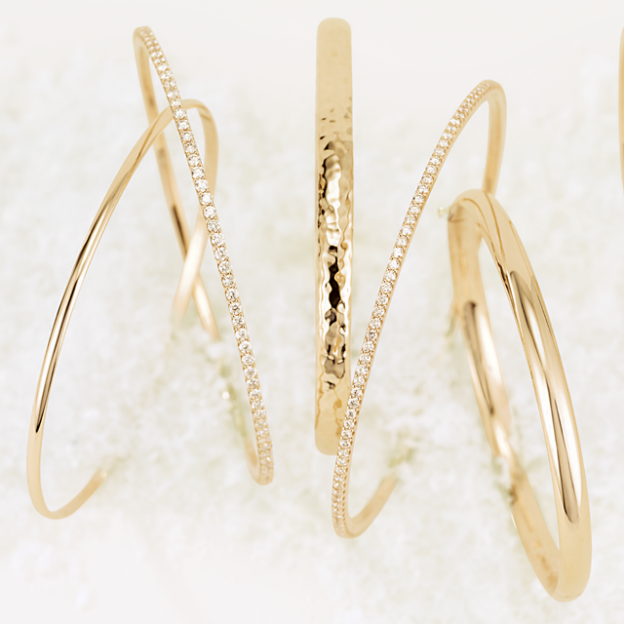
Custom bracelets designed and crafted by Jenni Stuart.
I’ve always worked under other people and other artists to get a handle on production and how the industry works and that sort of thing. The last woman I worked for realized that she needed a new website, so that meant building every piece in a cohesive engagement collection in every color metal, in every shape set in stone, and setting them all and photographing them all. It never would have happened. We’d still be talking about it to this day.
CAD (computer aided design) presented itself as a solution to that problem. One of the best jewelry suppliers in the country teamed up with Gem Vision and they built a program that’s based on Rhino 5 called Matrix. It is Rhino 5, but it’s got a crazy plug-in to it that has a lot of built in short cuts for jewelry, things like pre-built gems in every size and shape you can think of, pre-building the types of prongs that jewelers use over and over again, etc. It’s still Rhino, it’s just that they programmed a lot of jewelry-specific things into it, which makes it really easy to use.
We ended up buying the program and I taught myself how to use it and we built a new website, allowing for some major business growth.
Dave Moran: What led you to join the GrabCAD Community?
Jenni Stuart: I didn’t take any courses in CAD. I learned Matrix by reading the manual that came with it, and when I started striking out on my own I switched to Rhino, which is not geared towards jewelers. It’s more technical and a little bit more dry. There were shortcuts in Matrix that I no longer had, and one of the biggest was the gemstones. I don’t even know how to go about building a gemstone correctly with the facets in it and everything. So I Googled “3D faceted gem files” and the GrabCAD Community Library was one of the first results.
I just happened to find this file that I use on a daily basis at this point. I was amazed because the Library had a bunch of pre-built faceted gems, not only in all of the basic shapes but also some of the quirkier ones, which can be the hardest to work with because someone might come to you with an odd gemstone and want you to build a piece to fit it. I use GrabCAD all the time, now!
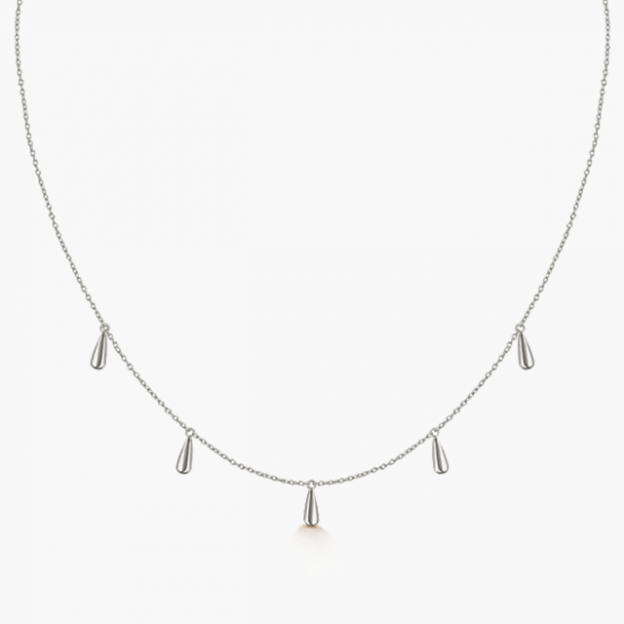
A custom necklace designed and crafted by Jenni Stuart.
And the Tutorials are amazing just because I’m really kind of flying blind here. I learn things as I need them, not in any structured formal way, so being able to find a tutorial that can help me figure that out is huge.
Dave Moran: When you’re searching for a gem, what are some of the terms you search for?
Jenni Stuart: If I need a gem, which is not that common anymore since I have an amazing master file at this point, I typically just search through the Community now. But I’ve been trying to teach myself how to render lately, so I’ll just search for terms like “Jewelry,” or “Ring,” or “Diamond.” Whatever material I am trying to render is the one I’ll hunt for. If I’m trying to get a good color yellow gold I’ll search “Gold Ring” and normally a few options come up.
Dave Moran: Tell me about your 3D printing process itself? I understand you outsource all of your prints through a service bureau?
Jenni Stuart: Once the design is done, I can just build the file in Rhino and I pre-cut for any stones I might need to set so I can do a lot of that “hand” work to finish the piece in CAD, which is phenomenal for me. I then send that file to Zero Porosity Casting in Waltham, Mass. They are incredible. They print it in a castable polymer. This castable polymer burns clean, so they cast it using traditional lost wax casting. The print is destroyed in the process, so everything is kind of a one-off, which is good for custom design. People like to feel like it’s one of a kind.
Dave Moran: Do you then show the model to your client before you go and make their piece?
Jenni Stuart: Because they do the printing and casting in-house, and the print is destroyed in the process of casting, I normally never even see the print unless I ask them to send it to me first. I’ve had one client in three years ask to see the print before we moved forward, but she was very particular about the design decisions she’d made and it was great to be able to do that just paying a printing fee, rather than having to use a piece of platinum, in case something had gone wrong.
Dave Moran: Is that why you’re currently trying to learn rendering, so you can show the designs to your clients before you start making a piece?
Jenni Stuart: It’s definitely hugely helpful. My next big mission on GrabCAD is to teach myself how to do that rendering because I’d prefer showing it to clients in the actual materials, as opposed to the raw, clay-looking prototype with lots of lines and wire-frames showing. People get very confused by that.
Dave Moran: You said you mostly do your designs for a piece in CAD now rather than by hand, so how much time does CAD typically save you?
Jenni Stuart: I’m so much faster than I used to be. I think the first ring I did, the first week when I was learning how to use the software, probably took about two days. Now, I can have a ring built for you in two hours. Normally, I’ll narrow down the design details with sketches so I don’t invest the time on CAD until I have a more clear direction with clients, and then I’ll build the first one and we’ll go from there. I’m good at sketching, but I can’t possibly be as precise as the computer is. My sketch gets a general design idea down, but not necessarily the perfect proportions. Being able to show people in CAD this is actually how big that stone is next to this one is huge. It saves me having to rebuild pieces or that kind of thing.
Dave Moran: Where do you get the raw materials to build these pieces from?
Jenni Stuart: I work in platinum, gold, and sometimes silver. I’m super-picky about the ethical sourcing, though, because the jewelry industry has a really bad reputation for good reason. You’ve got swarmy salesmen and unethical sourcing and that sort of thing.
I try and eliminate all that. All of the metal I use is 100% recycled and comes from a refinery here in the U.S. that takes in and refines metal from electronics, medical devices, old jewelry, housewares. It’s crazy how much fine metal is actually out there in the world! Everyone’s iPhone has a little bit of diamond and a little bit of gold in it. Being able to take all of that in instead of throwing it out is so awesome. The diamonds I use are from Canada.
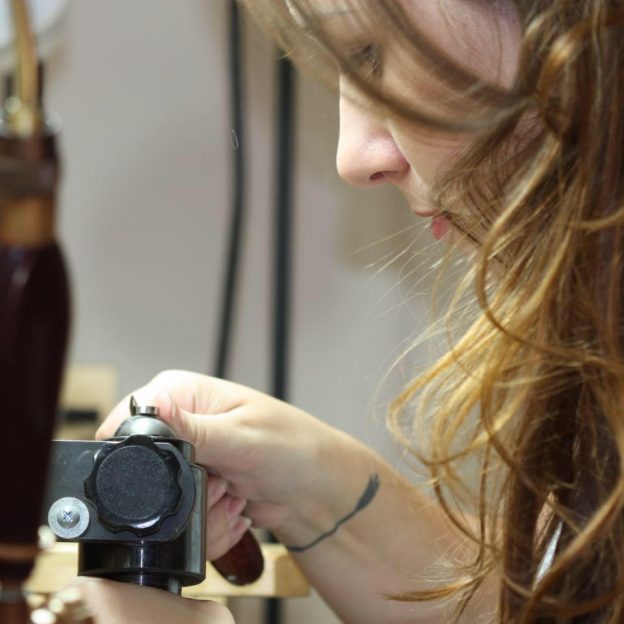
Jenni Stuart crafting a custom piece of jewelry.
Dave Moran: How many of your clients do you think realize that the physical jewelry they see, touch, and wear started as design in a 3D software program?
Jenni Stuart: It’s hard to tell. I think that they don’t know why what they’re looking at is different, but they can see the difference. Because I wasn’t taught how to use CAD and I never took any courses, I build in CAD the same way I build on the bench, so my work doesn’t feel as stiff and rigid as other mass-produced CAD jewelry. My pieces are really built by hand. I think if you were to ask a properly trained CAD professional, they’d probably tell you that they would take the map, and build the perfect curves, and run finished rails. I just build in simple solids and then use Cage Edit to manually manipulate them, because if I were to do it by hand I would use pliers to bend the wire to get the shape that I want, which is probably kind of amateur but it works for me.
Dave Moran: If you had to make a really intricate piece, would you do it by hand now or would you do it using CAD?
Jenni Stuart: I would do it with CAD now. The more intricate pieces tend to have more solder joints and more components, and that means more time on the bench (and more opportunity for things to go wrong). If it’s going to take me 20 hours to build something on the bench, you have to pay me for all of those hours. In CAD, it’s going to take me a couple of hours, so the price is going to be way better, it’s going to be way faster, the final piece is going to be mathematically flawless with no errors, and it’s one solid piece because of the way it’s printed. You don’t have any solder joints, so if it needs to be repaired down the line and you have to take a blowtorch to it you don’t have to worry about destroying that solder joint and ruining the entire piece. The structural integrity and the quality of the piece is fantastic.
Here are some of the other benefits of being a member of the GrabCAD Community.