3D printing continues to benefit the medical community in new and intriguing ways. It serves physicians and medical professionals in surgical assistance, helping them to create models of organs, bones, tissues, and joints, so their team can see, feel, and be familiar with them before they enter surgery.
3D-printed joints and organs offer the very best simulation to help them plan for what the actual surgery is going to be like once they make incisions and perform a complex operation.
It also provides new ways for manufacturers and product developers to create highly engineered and complex implants. Hospitals nowadays often have a 3D printing lab or department, integral to their organization.
Replicating a Realistic Model of the Human Heart
The models being built are increasingly more and more realistic to provide surgeons with more information and “feel” for the actual material they will encounter in an actual surgery.
At Carnegie Mellon's School of Engineering, Andrew Feinberg, professor of biomedical engineering, is using material science and engineering to provide a very lifelike model of a human heart that is most realistic, versatile, and has the actual characteristics of the organ.
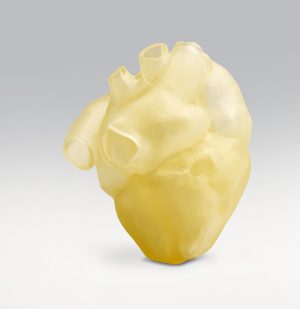
The Stratasys J750 Digital Anatomy 3D Printer has the power to create the look, feel, and function of real organs.
The heart his team created has a gel-like feel to it and is most like the actual human heart. It's made from a soft natural polymer called aliginate. This polymer gives it properties that are very similar to real cardiac tissue.
Having real-to-life properties enables surgeons to practice cutting, suturing, and manipulating the tissues in ways that are very similar to the actual heart that they're going to be operating on.
In order to make this heart, Feinberg built a new 3D printer that was custom-made to hold gel in a support bath large enough to print the desired size. He had to make some software changes that would speed up the printer and its capability.
3D Printing Bone
If the heart isn't remarkable enough, how about using a 3D printer to print actual human bone? Scientists at a university in Sydney, Australia, developed a ceramic-based ink that allows them to alter the future by 3D printing human bone.
What's even more remarkable about the 3D-printed bones is that they contain living cells that could be used to repair damaged bone tissue.
The researchers use a 3D printer with special ink containing calcium phosphate. They developed a technique called ceramic omnidirectional bioprinting in cell-suspensions (COBICS). This bioprinting method enables them to print bone-like structures that are hard in just a matter of minutes once they're placed in water.
Printing structures that resemble and mirror the qualities of bone isn't entirely new. However, this material allows the printed bone to be used at room temperature with living cells. It's also made without harsh chemicals or radiation.
These are all unique breakthroughs in the development of bone and closely mimic bone tissue. The surgeons believe that it could be used in clinical applications where there’s a demand for repair of in-place bone defects. It may also be used in a trauma situation or for cancer patients or where a big piece of tissue might be rejected.
More Realistic than Routine Imaging
3D printing is used to create many lifelike models that replicate human organs and tissues. Such organs are used to help strategize and communicate what's to be done by the surgical team. However, a 3D organ can also be printed that's very accurate, and even in some cases more accurate than traditional imaging methods.
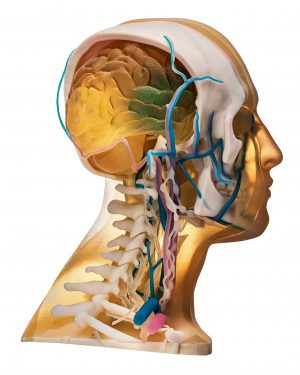
Stratasys Direct collaborates with healthcare and medical device companies to deliver visual and functional anatomical models to improve patient care and outcomes.
Creating such models in the past has been time-consuming and laborious, and not precisely accurate enough to substitute for other methods of imaging used in diagnosis and analysis. Now researchers are developing a method that's fast but also creates detailed physical models that are very precise. This model may then be used to diagnose, explain, and build a strategy around how they're going to treat an organ, joint, or tissue.
Finding Solutions to Hard Problems
Within today's modern health care facilities and treatment networks, 3D printing also helps create better parts and components of medical equipment to better treat patients. That's precisely what happened when the University of Michigan research teams worked on a solution to allow them to quickly develop an efficient and affordable way to expand ventilator capacity from one ventilator to more than one patient.
They created a device using 3D printing to mimic a scuba tank regulator. The regulator allows different pressures from one ventilator to be delivered to various patients with differing lung capacities and biophysical characteristics. This is quite useful because patients demand different volumes of air.
Because there was a shortage of ventilators, they could use one ventilator for more than one patient and therefore, accommodate any surge in demand for ventilators during the coronavirus pandemic.
The device that they created enabled this ventilator to double its duty. In addition, it was inexpensive, lightweight, very mobile, and easy to deploy to different locations.
New 3D Printing Solutions
There are numerous ways in which 3D printing is changing the face of medicine. It provides new solutions with new options or can create complex implants compatible with the challenges of biomedicine. 3D printing labs within hospitals and health care networks are more able nowadays to fabricate within their own facility, in short order, to solve problems that would ordinarily take months if not years to develop.