Rapid prototyping has made positive impacts across various industries such as automotive, medical, and commercial goods which has led to some companies wanting to scale their additive manufacturing capabilities past prototyping and into production. In the past 30 years, additive manufacturing has been in a constant state of growth and development. The most common method of 3D printing had been Fusion Deposition Modeling (FDM). This is what propelled additive manufacturing into its current role of rapid prototyping.
The question on many industry leaders' minds however is whether or not additive manufacturing has reached the heights needed to shed its past identity of prototyping powerhouse.
In short the answer is yes and we get into the reasons below.
Hardware Advancements
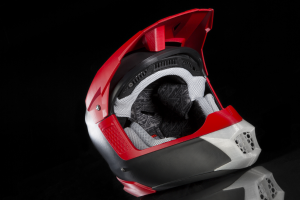
Prototype Motorcycle helmet printed using the Stratasys Fortus 450
Additive manufacturing in its infancy relied on a select few technologies to fabricate parts. This includes methods like Fusion Deposition Modelling (FDM) and Stereolithography (SLA). These technologies have since become more accessible to hobbyists, students, and smaller companies rather than only being used by companies with significant amounts of money.
On a more significant level, more complex and varied printing technologies have cropped up, bringing the total ways to print to 8.
Of these 8 methods, Selective Laser Sintering (SLA) , Polyjet (PJ), Direct Metal Laser Sintering (DMLS), and Electron Beam Melting (EBM) have enabled companies to print using materials beyond basic thermoplastics. As for the other long existing technologies, they have become more consistent in their quality and become faster in producing parts.
Material Advancements
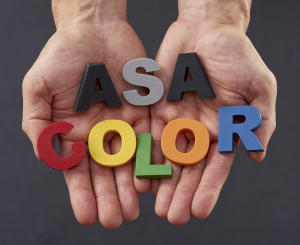
Multicolored letters printed in ASA
Expanding on how 3D printers have allowed for more selections of materials to be used. Thermoplastics like ABS, ASA, or PLA have been the main way 3D printers have been fabricating parts. These materials are readily available, cheap, and just sturdy enough for the purpose of prototyping but material sciences have advanced to allow for 3D printed parts to be production grade quality.
In the industrial, automotive, and aerospace industries, materials like carbon fibre have become possible for 3D printing to utilise. Within the fields of medicine, consumer goods, and even fashion, resin based materials have allowed for hyper realism in medical models that are also human and food safe. Metal based 3D printing has recently gained prominence and is poised to produce high-quality production parts.
Software Advancements
Producing parts is ultimately a small part of the equation when it comes to manufacturing. Distribution, manufacturing execution, preventative maintenance, and order tracking are what takes a simple collection of printers, and turns them into a manufacturing powerhouse. Advancements in software such as machine learning and IoT have found their way into the additive manufacturing world. These printers with their advanced materials now have the ability to leverage data and more importantly connect to a network. Software has the ability to further push additive manufacturing towards manufacturing at scale.
If you would like to learn how a robust software driven platform can allow additive manufacturing to assume it’s role on the factory floor alongside traditional manufacturing, download our industry report!