Throughout 2023, supply chains will continue to experience challenges and delays, affecting production and shipments worldwide.
According to PR Newswire, Coupa Software found that 82% of supply chain leaders believe that these problems will remain the same or become even worse over the next 6-12 months.
During 2022, four out of five organizations experienced one notable supply chain issue and 50% experienced three or more setbacks.
Is this starting to sound familiar?
Do you feel like we are living in a strange, recurring Groundhog Day?
If so, Dr. Madhav Durbha, Vice President of Supply Chain Innovation at Coupa agrees with you. He believes that, “with climate change and geopolitical tensions expected to impact food and cause disruptions, now is the time for supply chain leaders to take initiative and be creative as to how they can invest and improve their operations.”
So how can we resolve these supply chain delays?
By utilizing additive manufacturing, companies can control output and will no longer have to rely on the supply chain.
Cheaper and quicker prototypes
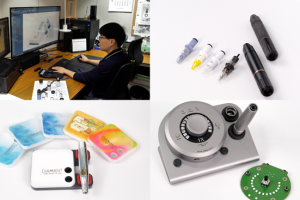
Semi-permanent makeup machine and needles
Additive manufacturing enables businesses to prototype products and designs faster, resulting in greater cost-efficiency. After utilizing the Stratasys J55 Prime 3D printer, SEONG YUN TECH decreased the cost of prototyping from KRW 10 million to KRW 100,000.
Since their manufacturing schedule was shortened from a month to a few days, SEONG YUN TECH implemented design changes immediately. With this quick turnaround, the semi-permanent makeup machine models were ready within two to three days.
According to the CEO of SEONG YUN TECH, Dongmin Lee, “using Stratasys’ 3D printers delivered tremendous synergy in product development, and these printers have been essential for the company’s development. We experienced that expanding into additive manufacturing enhances the agility of product planning and manufacturing.”
Overcome part shortages
When Stratasys first began producing the H350™ 3D printers, the PCB Stepper Controller Board was discontinued due to COVID-19 delays. Since this was vital for the printer to operate correctly, the team replaced the part with a different electronics board. The only drawback was that this new board required air cooling.
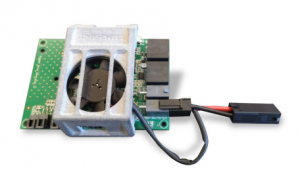
Circuit board bracket
In order to solve this problem, the H350 Production team used the H350 3D printer to produce a circuit board bracket. This part easily secures a fan to the electronics board. The bracket doesn’t need any tools or screws, streamlining product assembly. By printing this optimized part in-house, production for the H350 could continue and was no longer affected by supply chain delays.
Another instance when the H350 effectively resolved shipping issues was in March 2021. Eighty large housing parts were stuck on the Ever Given container ship in the Suez Canal. Philipp Götz, CEO of Götz Maschinenbau, a mechanical engineering company, was asked by one of his customers for assistance. With the H350, Götz was able to finish this order in only two weeks, enabling his customer to complete their machines and meet required deadlines.
Instantly print replacement parts
Each month, at Siemens Mobility’s flagship site RRX Rail Service Center, a hundred trains enter and leave the depot. In order to be equipped for issues and maintain flexibility, Siemens utilizes the Stratasys Fortus 450mc 3D printer.
As a Siemens representative stated, “this is where FDM additive manufacturing fits in perfectly. [It provides] us with the capability to rapidly and cost-effectively produce one-off, customized production parts.”
Parts print within hours, as compared to the weeks or months it may take with casting. According to Tina Eufinger, Siemens Mobility Division, “within a week, we can iterate and optimize the design. [And] then 3D print a final, customized production-grade part. This has [allowed] us to reduce the manufacturing time of each part by up to 95%. [This] has significantly sped up our ability to respond to customers.” This is essential in the railway industry since repairs are constantly required, typically after an accident.
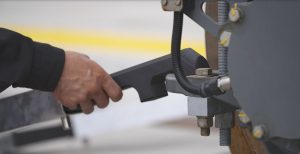
Siemens 3D printed tool
Taking matters into their own hands
Additive manufacturing allows suppliers to break free from their reliance on supply chains and finally end this Groundhog Day-esque cycle.
By printing in-house and on-demand, companies can gain control over their operations and production.
Whether it be prototypes, acquiring that last part, or repairs, additive manufacturing enables companies to be self-sufficient.