One of the greatest myths that exists within the 3D printing and additive manufacturing (AM) sphere is, “you can make anything.”
This myth almost certainly derives from one of the unquestionable advantages of 3D printing, namely the ability to produce parts and products with unprecedented complexity that simply could not be made in any other way, or, if they “could” be manufactured using traditional methodology, the time and cost constraints of doing so would be too great to justify.
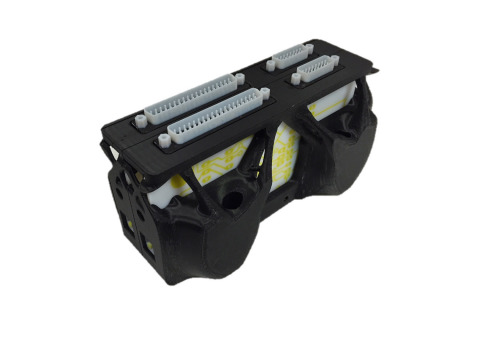
The weight of this Stratasys 3D printed circuit box for space applications was reduced by 30% using SIMULIA design optimization.
The common nature of different 3D printing processes, specifically building up parts additively, one layer at a time, sets them firmly apart from other, traditional manufacturing processes that are subtractive in nature. It is this fundamental capability that permits additive processes to build complex geometries.
However, it is also important to understand that the different AM processes vary in nature, too. Like any other manufacturing process, they are each subject to technology and process constraints. These constraints involve a different set of rules than encountered for traditional manufacturing methods, but essentially acknowledging and following these rules ensures higher quality, more cost-effective 3D printed parts.
The concept of design for manufacture (DfM) is not a new one in that the method of manufacture is considered during the entire design and development stages of products and parts in order to optimize their functionality in relation to the way they will be produced and subsequently assembled and tested. This considered approach results in higher quality parts, with shorter overall product development times (faster to market) and is more likely to eliminate costly mistakes in tooling and/or production.
Thus, the fact that successful AM applications benefit greatly from adhering specifically to DfAM (design for additive manufacturing) should come as no surprise.
As interest continues to grow in additive manufacturing as a tooling and true production process, with parallel adoption increases, there is also an increase in demand for designers with specific DfAM skills. Currently they are in short supply — but this skill set is essential for more widespread adoption of AM.
The difficulty comes from the fact that learning DfAM is not just an extension of DfM. DfAM demands a fundamentally different approach — relearning from scratch and putting DfM knowledge to one side.
Of course, 3D printing and AM can be used economically to produce straightforward parts, but as stated, one of the major benefits is the ability to build complex geometries. Thus DfAM opens up new opportunities for manufacturers — with specific time and cost benefits — in two main areas: part consolidation and topology optimization. However, there are specific challenges too.
Benefits
Consolidation of assemblies into a single part.
One of the major constraints of traditional manufacturing is the “manufacturability” of complex components, which often means they have to be broken down into multiple parts to make manufacturing possible and then subsequently assembled. AM is demonstrably able to overcome this issue — the go to example here is the GE Leap engine fuel nozzle. This is a much used case study that shows how a complex assembly component for the Leap Engine, comprising 18 individual parts, was consolidated into a single part, that was qualified and now produced in medium volumes on a series of metal AM platforms for GE Aviation. There have been other public domain projects, in the aerospace and automotive sectors in particular, that highlight these capabilities, but few, if any others are publicly qualified and shown to be in production.
It takes serious design experience and understanding to be able to do this, and it requires software tools that can keep up. This is one of the challenges for AM actually, software that can keep up!
Topology Optimization
Many structural components are designed with more material, and thus weight, than they actually require. In turn this can mean increased and unnecessary loads on moving parts and compromised energy efficiency during use. AM enables the design — and production — of parts with highly efficient strength to weight ratios that also result in material savings. Moreover, topology optimisation for AM parts allows designers to specify loads and supports within a part to achieve full — often improved — functionality.
This type of optimisation can be achieved using lattice structures, for example. Understanding the AM process (whichever one you choose), and designing within the parameters of that process will lead to more efficient parts, improved strength and durability, while also reducing costs and improving safety. Done correctly, it’s a win/win/win.
Challenges
Software
As alluded to above, the software ecosystem for DfAM is notoriously struggling to keep up with AM hardware capabilities. I say “software ecosystem” because it is not just about the design process itself but also the functions of optimization, simulation, and support generation. There is a tremendous amount of activity in this area, however the big 3D software players — Siemens, Dassault and Autodesk — are seriously ramping up, with improved functionality being added month on month, it seems. There are also specific AM software add-ons emerging at a similar rate too, from smaller players with specific knowledge and expertise — Materialise, 3D SIM, OnShape, Ansys/SpaceClaim are just a few that spring to mind. GrabCAD is also developing its own 3D printing software solution, GrabCAD Print. In addition, the progress of generative design programs is increasing too.
Overhangs and Support Structures
When designing for AM, overhangs, and the prerequisite support structures to enable their production with AM are two fundamental issues. Many industrial 3D printing processes struggle with overhang features and require supports as they are built. Thus, when designing a part that will be additively manufactured, design skills must also be applied to the nature and placement of support structures. Designing minimal but functional supports to optimize the final part demands a new design skill set, and often some lateral thinking by designers. There are numerous software packages that include the automatic production of support structures, many hardware vendors are working on this — unilaterally and/or through partnerships with software companies.
Internal stress
Another challenge for AM processes, most notably with metal materials, is the resulting internal stresses within a part. This is caused by the rapid heating and cooling of the powdered material during the build process and it can affect the mechanical properties of the final part. However, skilled designers can minimize the effects of internal stress by applying build orientation rules to maximize the cross-section of each layer and disperse the heat more evenly/effectively.
In Summary
The opportunities and the challenges of DfAM, as with most things, amount to a series of checks and balances. There is much to be gained if approached with the right knowledge and skills, and enabled by the correct tools. As ever, it also comes down to identifying the right applications to maximise the potential of AM.
Like what you've just read? Sign up to receive GrabCAD's free weekly Digital Thread newsletter.