When it comes to automotive manufacturing, 3D printing is becoming more prominent. In fact, 3D printing and cars have a long history that’s only becoming deeper. At the moment, you’re not likely to get a car which has been made completely by any additive manufacturing companies, although there are some niche vehicles which are.
The mainstream automotive industry is adopting 3D printing in varied and more limited ways, but it’s still becoming a more integral part of making cars. It’s also important to note that automakers sometimes guard manufacturing techniques, and some automakers openly talk about them.
In this blog post, we highlight the automakers who are really diving into 3D printing for manufacturing.
Ford
One of the biggest promoters of 3D printing in the automotive industry has been Ford. The Dearborn, Michigan-based automaker has been using the tech since the 1980s, making it an early adopter.
Among the latest 3D manufacturing techniques Ford has been pioneering is using the Stratasys Infinite Build 3D Printing System. This tech has been in use at the Ford Research and Innovation Center, which is located in Metro Detroit.
One of the driving forces behind Ford’s increased use of 3D printing comes from the need for light-weighting in vehicle designs. Thanks to the unique structural properties, additive manufactured parts oftentimes weigh less than traditionally-made car parts. That means better fuel efficiency, something which is an issue not only in North America but also other markets around the world. In some cases, Ford engineers have found a printed part can weigh as much as half that of a traditional component.
Ford has used 3D printing successfully in a few other areas. For example, low-volume vehicle components cost less if printed versus using more traditional methods. This is an increasingly common practice for many Ford Performance parts, which are used exclusively on models like the Explorer ST.
Prototypes and concept vehicles are another strong fit for printing parts. Depending on the exact parts being used, Ford engineers will sometimes choose to print unique components since it is much faster and costs significantly less.
BMW
One of the top German automakers, BMW, is also one of the top car brands for 3D printing. Many examples of BMW 3D printed parts are showcased in the i8 Roadster.
Normally, the different components for the folding hardtop would weigh quite a bit. Not only does that harm fuel efficiency, which is one of the claims to fame for the car, they also shift the vehicle’s center of gravity so much that handling suffers and the risk of rollovers increases significantly. By using printed parts for the i8 Roadster’s roof mechanism, BMW was able to preserve the nimble, crisp handling of the car and cut down on overall additional weight.
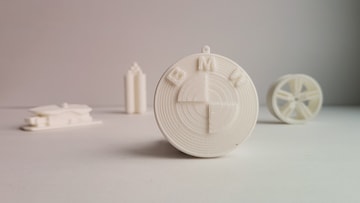
Source: BMW.com
BMW is serious about additive manufacturing. It revealed last year that a new additive manufacturing campus is being built in Oberschleissheim, in the same area where it has a cutting-edge Autonomous Driving Campus. The new facility will cost 10 million Euros to build.
BMW also owns Mini, which has also been using 3D printed parts with great success. The British brand has always showcased how customizable its cars are from the factory, something which appeals to people who want to drive something unique.
To push this aspect even further, the Mini Yours Customized program was created last year; it allows Mini owners to order certain components such as a door sill plate or light cover with a completely custom design, phrase, or even their name integrated into it.
Normally, such a program is only reserved for ultra-expensive vehicles like a Rolls-Royce Phantom. Thanks to the wonders of additive manufacturing, Mini can offer customized components for relatively affordable prices, plus get them into the hands of car owners sooner.
Audi
The Audi 3D printed car was revealed back in November of 2015. While not a production model, the 1:2-scale reproduction of an old Auto Union race car was created to generate buzz around the German automaker’s additive manufacturing tech.
More recently, Audi has opened a completely separate 3D printing department, showing it’s serious about leveraging the tech. Like Ford, Audi is using printers to manufacture prototype components and some consumer vehicle parts.
But that’s not all.
Perhaps the most valuable function of the Audi 3D printing department comes into play when any tooling on an assembly line breaks; instead of waiting for a supplier to ship a replacement (which can sometimes take days) the automaker can print one and have it installed in a matter of hours. Considering how much revenue each hour of downtime costs Audi, this helps reduce operational costs and boost profits.
Porsche
Porsche, Audi’s sister company, has also been making serious headway with 3D printing. Most of the concentration has been on old cars, or more specifically the Porsche Classic division.
Collectors pour considerable resources into preserving and restoring historic models, but sometimes components are nowhere to be found. To help, Porsche Classic is now manufacturing those parts using 3D printing. It’s a strange and wonderful marriage between old and new, showing how just because we forge ahead with cutting-edge technologies doesn’t necessarily kill everything from the past.
To read more on 3D printing in the automotive industry check out: