I have always admired designers and their work. Designers have both the creativity and the freedom to design whatever they can imagine. Something I, as mechanical design engineer, didn’t always have in my job description. When I started working in the new product development industry, I was lucky enough to work both as designer and engineer.
As a product designer I had freedom in design process, but as an engineer I am limited with design for function and design for manufacturing. Also, as good engineer you must pay attention to the economics side of parts production and cost effectiveness. Those factors limit creativity and engineering design freedom.
From the very start, we as mechanical engineers are taught to design parts as simply as possible – square and chunky – so the parts can be economically manufactured. This was due to the limit of available manufacturing technology. Today, however, everything has changed with 3D printing. One of the reasons why I love 3D printing is that it allows me the freedom to design and creatively solve engineering problems.
The art of engineering design
Earlier this year, GrabCAD hosted a challenge where participants had to design an airplane bracket for additive manufacturing. I followed this challenge with a lot of interest to see what creative designs engineers could come up with.
I was pleasantly surprised with the results. So many of you unleashed serious creativity in your final bracket designs. One of my favorite designs was Bracketosaurus Rex by Nic, even it was not a finalist. In the future we could see more bone like designs and more use of biomimicry. This way, simple, boring mechanical parts like brackets can become masterpieces in the mind of a skillful engineer.

Heat Exchanger designed by Autodesk & created by EOS via EOS press kit
It’s not only mechanical parts that can benefit from engineering creativity. Here is another one of my favorites example of engineering creativity, a heat exchanger. This heat exchanger is designed by Autodesk and produced with EOS DMLS technology. The geometry is optimized for maximum heat transfer with turbulators inside cooling tubes which disrupts the flow of the cooled fluid. A part like this is impossible to make with traditional manufacturing technologies such as CNC machining or casting. It’s a true example of engineering design optimized and accurate for additive manufacturing.
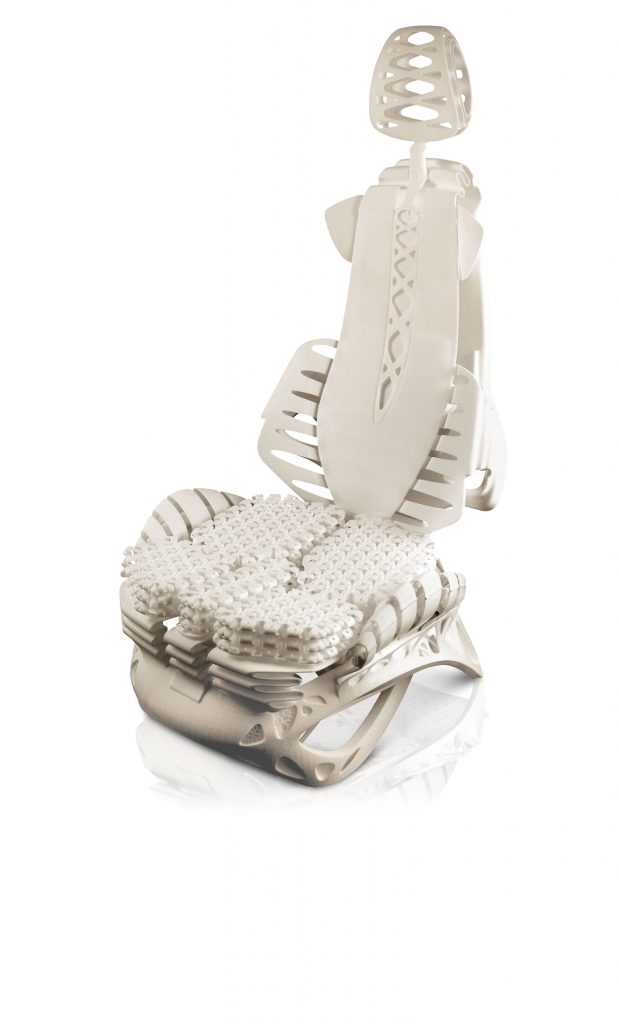
Automotive seat produced as single piece with all moving parts via EOS press kit
The design is not only for the parts, it’s also for assemblies. I hope that everyone remembers the heart gearbox that appeared everywhere when the 3D printing hype first started. You can design the whole assembly with moving parts and produce it as a single piece with 3D printing.
Now this is the ultimate level of creativity and design skills for engineers. A great example of this method is presented with this automotive seat concept. The whole seat assembly is designed with moving parts and made with SLS 3D printing technology. The seat has little springs as part of the whole design. The spring produces a soft feeling when sitting on the seat and amortized bumps while driving. A true masterpiece of engineering art.
New software tools for engineering creativity
As you can imagine this kind of complex geometry requires some serious modeling skills to make. Using traditional CAD software everyone could have difficult time to model this 3D models. This is why some of the new software tools are developed to help engineers create complex and creative geometries.
One of such tools is Solidthinking Inspire. It is mixed software with FEM analysis and 3D modeling tools. In the traditional way, you would create a 3D model with geometry, put it into FEM analysis, then after some iterations and design changes get final design of the part. Inspire workflow is other way around, it’s rather reverse. You start with the basic geometry shape and initial conditions, and the software do the rest.
Based on constraints, forces, and material type set in initial conditions, the software calculates and creates optimized geometry guidelines of the part. By following software generated guidelines the geometry you design should produce a 3D model with optimized topology.
What I’m most excited about is announcement from Autodesk for their project Dreamcatcher, a generative design system. This means that software based on initial condition generates geometry that meets certain requirements. But furthermore, the software doesn’t generate only one design, it generate hundreds of possible options. This gives you variety of design options to choose. With more options to work you can also have more inspiration for final design. As Jeff Kowalski stated, current CAD stands for "Computer Aided Documenting." This new software will be truly "Computer Aided Design."
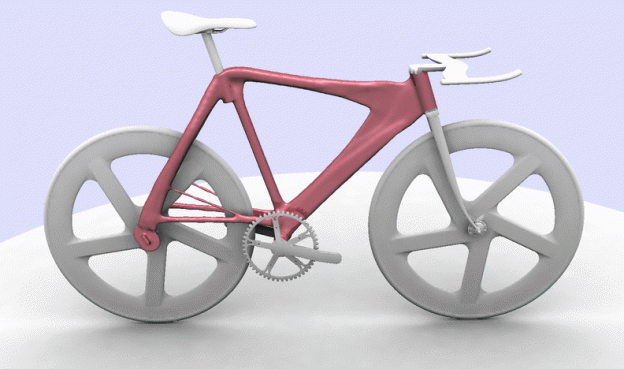
Bike frame generated design with Autodesk Dreamcatcher
The future of engineering design
What does all of this mean for mechanical engineers? Will advanced software AI and direct digital fabrication replace the need for engineers, or will it just make our job better?
I know it will make it better. We all are gonna be more like Tony Stark working with hands in a holodesk while Jarvis will provide with parts design proposals, leaving us to take and create the best possible solution. With this all 3D printing and new software technology been developed engineers will have all the right tools to advance to new level.
Our next level is to express our creativity in designing the parts with superior performances, no longer limited by manufacturing limitations. The time for engineers is coming, it is our time to shine and present our inner creative person, to truly show what art in engineering means.
We're making professional 3D printing easy and accessible
There's a new solution coming your way this summer. Click here or on the graphic to the left to request updates and beta access.