Additive manufacturing has been greatly impacting the automotive industry over recent years and the NERA e-motorcycle is just one example of 3D printing technology innovation in this arena (and at its finest).
From being able to create state-of-the-art prototype components to having fully 3D printed vehicles, printing a motorcycle is yet another milestone for additive manufacturing and the transportation industry.
In this blog we’ll be delving into the incentives behind the creation of the NERA 3D bike design, the design process itself and the wider implications of its creation on the automotive industry at large.
The brains behind the NERA e-motorcycle
German additive manufacturing company BigRep revealed the NERA e-motorcycle back in 2018, making it the first time that 3D printing was brought into motorcycle production.
This revolutionary bike, created by the company’s innovation team, NOWlab, was designed by Marco Mattia Cristofori
and Maximilian Sedlak. It’s fully 3D printed (aside from some of the internal components), highly flexible, absorbs bumps better than most other motorbikes and uses just 15 parts to form the final product.
While not yet commercially available, it has set the benchmark for what can be created and what could be available at some point in the future.
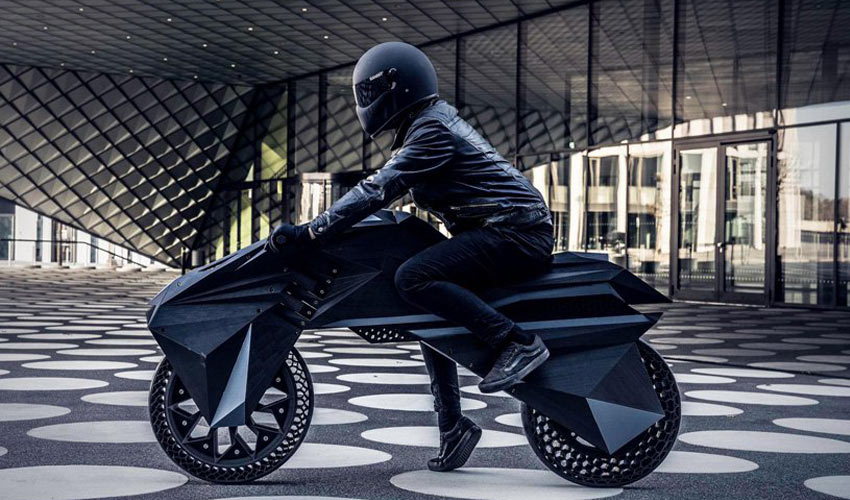
The NERA E-Motorcycle (Source: Bigrep)
What was the vision?
The NOWlab team set out with the primary goal of creating a functional prototype that revolutionized motorcycle mobility and did so using 3D printing techniques.
“We engineered NERA e-Bike from the ground up, disrupting traditional design, engineering and production in every aspect. The result is a 100-percent, customizable, functional prototype, designed and produced with more time and cost efficiency than previously imaginable,” says a BigRep source.
They added that 3D printing “changes the perception of design language and allows total freedom in terms of design: bionic, organic, edgy. Any design is only one thought away from reality.”
NOWlab co-founder Daniel Büning believes: "NERA illustrates the massive benefits that 3D-printing offers for the production of end-use parts, particularly for batch sizes between lot size one [small quantities manufactured in a single production run] to small series, by reducing lead times and costs, optimising supply chains and limiting dependency on supplier networks.”
The design and building process
NERA was 3D-printed using the fused filament fabrication (FFF) process, whereby a continuous filament of thermoplastic material is fed through a moving, heated printer extruder head.
Key design points for the NERA bike can be summarised by the following features:
- Relevant core parts that weren’t 3D printed such as the battery and control systems were arranged before designing the outer shell.
- The airless tires, bumper, custom fitted seat and handles were printed with flexible material which enabled them to utilise novel design approaches that replaced traditional mechanical components.
- A horizontally embedded Pro Flex suspensor with honeycomb structure replaced a traditional hydraulic system integrated in metal fork steering systems for motorcycles.
- Power stemmed from a rear, electric engine.
- The battery was fitted inside the angular body of the bike.
The low polygon/ stealth design of the outter shell avoids top layer. (Source: Bigrep)
The wider impact
The NERA bike represents a revolutionary approach to product development in both the automotive industry and other sectors, in terms of advancing digital simulation and custom manufacturing methods.
It’s fair to say that other design labs, universities, automotive companies and even at home enthusiasts may start to pursue 3d printing their own bikes and cars in future now that such a precedent has been set.
Indeed, designers, doctors and even architects have applied the bike’s design techniques to a number of products, from a steel bridge to models of patients' hearts that are used to plan surgery. MIT have adopted the technology to create 3D-printed inflatable structures for car interiors that could transform into different configurations with one click.
Conclusion
The adoption of additive manufacturing in the automotive industry brings countless benefits, including speeding up prototyping, greater opportunities for design innovation, reduced overall costs, simplifying the supply chain, the use of lighter parts (therefore reduced fuel costs) and greater potential for customization.
Indeed, some industry leaders predict 3D printing in the automotive industry will generate $9 billion in revenue by 2029. Big names including Audi and Porsche are adopting 3D printing techniques to design and produce their latest cars.
While the NERA bike boasts trailblazing features such as the airless tire, functional integration, and embedded sensor technology, you can’t buy one for yourself just yet. However, I have no doubt that 3D printed e-motorcycles will come to the market in the future, and it will be game changing.