Additive manufacturing has been adopted across various industries, from the automotive sector and the medical/dental world, to consumer goods and the education sphere. However, one sector where we’re seeing particularly impressive take-up is within aerospace.
3D printing allows for the faster and more efficient creation of a variety of parts with complex geometries, therefore reducing the need for expensive trial and error. It therefore comes as no surprise then that such technology is a big hit in today’s innovative aerospace landscape.
Aerospace – the branch of technology and industry concerned with both aviation and space flight – was in fact one of the first industries to invest in large scale 3D printing, with some aerospace companies adopting the technology as early as the 1980s. Fast forward to 2022, and the aerospace additive manufacturing market is estimated to be worth around $3 billion - predominantly due to the demand for lightweight aircraft engine parts.
In this blog we’ll be exploring how 3D printing is used within aerospace, some of the benefits of 3D printing within this context and delving into what some of the major aerospace companies are achieving right now.
The Astronomical Demand for 3D Printing
The cumulative demand for new aircraft has led to orders of nearly 38,000 new aircraft over the next 20 years. Equipment manufacturers, designers and suppliers need cost-effective solutions to produce these aircraft as quickly and efficiently as possible within the context of a highly regulated industry where safety and quality are key.
The four main areas in which 3D printing is used in the aerospace industry are jigs and fixtures, surrogates, mounting brackets and for detailed prototypes.
In addition to these more commonplace uses, 3D printing is also being used to make lighter and more efficient engines and turbine parts, lighter plane seats and even drones, to name but a few.
If you are interested in contributing to aerospace history? Check out our latest NASA challenge, where NASA is challenging the community to design innovative wind tunnel test sections that can increase the effectiveness of an advanced transonic wind tunnel facility.
What 3D Printing is Bringing to Aerospace
Due to the typically short runs of aircraft parts, the aerospace industry uses additive manufacturing for a great deal of its production. The technology can produce intricate parts that are more resilient and lightweight compared to those made using traditional techniques - an obvious bonus.
In fact, EOS states that additive manufacturing can produce weight reductions of between 40-60%. To put this in perspective, the average corporate aircraft travels 75,000 miles per month. A single component that is designed and manufactured with 3D printing (and is therefore lighter), reduces air drag by 2.1%, which in turn reduces fuel costs by 5.41%. By cutting fuel and limiting emissions, 3D printing can subsequently help to minimize the environmental impact of air travel. In an age of heightened environmental awareness, this couldn’t be more on trend in terms of long term company strategy and consumer priority.
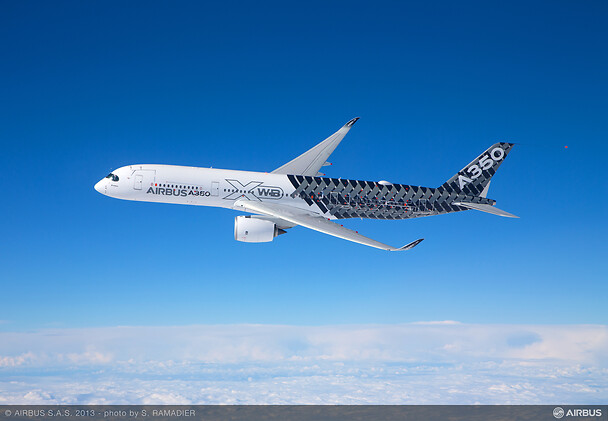
The Airbus A350 XWB (Source: Airbus)
In addition, 3D printing can produce hundreds of thousands of parts without relying on expensive tooling changes involved with traditional manufacturing processes. “Tool-less” production requires less energy, since modified parts or upgrades can be produced as needed, alleviating the need for costly storage.
Aerospace parts often include internal channels for conformal cooling, internal features, thin walls and complex curved surfaces. 3D printing processes are able to manufacture such features and create highly complex and lightweight structures with high stability, whilst allowing for the consolidation of multiple parts into a single component. This leads to further cost reduction, reduced waste, faster production times, greater consistency and better surface finishes across aircraft.
“From a full-size landing gear enclosure printed rapidly with low-cost FDM, to a high-detail, full-color control board concept model, there is a 3D printing process suited to every prototyping need”, explains Vice President of Operations for North America at PrintForm, Bill Artley.
What are some of the latest 3D printed innovations within aerospace?
NASA
- Archinaut: After 3D printing over 200 astronaut tools and devices from a manufacturing unit aboard the ISS, start-up company Made In Space
The Perseverance Rover (Source: NASA)
received a $73.7 million contract from NASA to explore 3D printing a small spacecraft called Archinaut One in orbit. The spacecraft is set to be ready for launch sometime later this year.
- Rocket engine hardware: NASA recently completed te
- sting rocket engine parts with Aerojet Rocketdyne, a California based manufacturer that uses metal 3D printing methods.
- Exploration rover on Mars: The Perseverance Rover a.k.a Percy has 11 3D printed metal components.Five of them, printed using titanium, make up the shell of the PIXL instrument that looks for signs of fossilized microbial life on Mars. The other six nickel superalloy parts are within the MOXIE heat exchangers, which create oxygen.
- 3D printing on the Moon: 3D printing house company Icon has been granted funding to develop a space based construction system that could potentially allow for the support of future habitats on the moon. “Building humanity’s first home on another world will be the most ambitious construction project in human history and will push science, engineering, technology, and architecture to literal new heights,” said Jason Ballard, co-founder, and CEO of ICON.
Boeing
- ‘WGS- 11 satellite: Aerospace manufacturer Boeing has begun using 3D printing in its production of a Wideband Global SATCOM or ‘WGS’ satellite for the United States Space Force as part of a $605 million contract. The system offers much greater mission support and anti-jamming capabilities than its predecessors.
- New jets: The new Boeing 777x is equipped with two GE9X engines. Besides the fuel nozzle, the engine incorporates more than 300 printed parts. This reduces the engine’s weight and makes it the most efficient twin-engine jet in the world with fuel consumption lowered by 12 % and operating costs lowered by 10 %.
Airbus
- 3D printed aircraft parts: Complex 3D printed components continue to be installed in Airbus’s aircrafts. Indeed, the Airbus A350 XWB contains more than 1,000 3D printed parts.
- Neorizon: A partnership with San Francisco based start up Local Motors Industries will see Airbus focus on 3D printed drones and 3D printed self-driving cars, potentially shortening lengthy supply chains via the ability to create such entities at scale.
Lockheed Martin
- Lunar rover project: The American aerospace and defense company regularly uses 3D printing as part of their space explorations. They invested in a Makerbot Method X to print a number of parts for the rover project on the moon. It enables whole parts to be designed, printed and tested all in the space of a single day, with a new iteration ready for testing soon after.
The Rolls Royce Pearl 700 engine (Source: Rolls Royce)
Rolls Royce
- Pearl 700 engine: With testing now complete, the Pearl 700 engine (which can produce more than 18,000 pounds of thrust and deliver significant increases in efficiency) is moving into the production phase. 3D printing of the combustor tiles allows for optimized and complex shapes whilst saving on weight when they are eventually fitted into the ultra-long range Gulfstream G700.
Final Take Off and Thoughts
As time goes on, additive manufacturing is being used to design more and more everyday items, but it’s also being utilized on the bigger stage of aerospace.
Current US president Joseph Biden recently called 3D printing “incredible”. He added: “it can reduce part lead times by as much as 90%, slash material costs by 90%, and cut energy use in half. That all lowers the cost of making goods here in America.”
Rich Garrity, President, Americas at Stratasys, the large 3D printer and material maker said: “Stratasys has been leading the shift to additive manufacturing at production-scale for large manufacturers like GM, Boeing, and Lockheed Martin. This new AM Forward initiative is a great way to help give small- to medium-sized manufacturers the confidence to invest in production-scale additive manufacturing technologies and expertise. It is a further signal that we have reached an inflection point in the use of 3D printing in manufacturing applications.”
When it comes to additive manufacturing and the aerospace realm, the sky really doesn’t seem to be the limit.